manual control
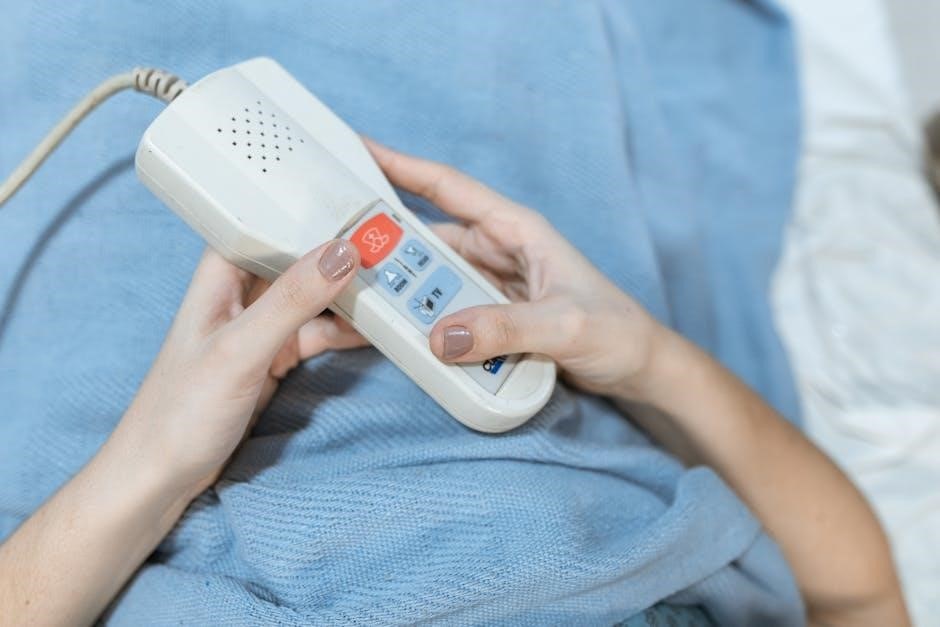
Manual control involves human intervention in system operations, relying on expertise and real-time decisions․ It is essential in various engineering fields, ensuring adaptability and precision in dynamic environments․
1․1 Definition and Scope of Manual Control
Manual control refers to systems where human operators directly regulate processes through real-time decisions and physical interventions․ It relies on expertise and adaptability, often in dynamic or unpredictable environments․ The scope encompasses various engineering domains, including industrial automation, aerospace, and robotics, where precise adjustments and immediate feedback are crucial․ Manual control systems are essential for tasks requiring flexibility, such as fine-tuning parameters or handling exceptions that automated systems cannot manage effectively․
1․2 Historical Development of Manual Control Systems
Manual control systems trace their origins to ancient mechanical devices, such as water clocks and millstone regulators․ The Industrial Revolution introduced manual levers and valves for machinery control․ By the 20th century, electronic systems emerged, enabling precise human intervention․ Modern advancements integrate manual control with digital interfaces, optimizing efficiency and safety․ This evolution reflects the enduring need for human oversight in complex systems, blending traditional methods with cutting-edge technology to meet industrial demands and ensure operational reliability․
1․3 Importance of Manual Control in Modern Engineering
Manual control remains vital in modern engineering for its adaptability and precision․ Engineers rely on manual systems for initial setup, calibration, and troubleshooting․ In critical applications, human expertise ensures safety and quick decision-making․ Manual control also complements automatic systems, providing redundancy during failures․ Its role in industrial automation, process industries, and robotics underscores its enduring relevance․ By integrating manual oversight with advanced technologies, modern engineering achieves a balance between efficiency and reliability, ensuring optimal performance across diverse sectors․
Fundamentals of Control Systems
Control systems involve inputs, outputs, and feedback loops to regulate processes․ Manual control relies on human operation, while automatic systems use algorithms․ Both ensure stability and accuracy․
2․1 Basic Components of Control Systems
Control systems consist of sensors, actuators, and control units․ Sensors detect system states, actuators execute commands, and control units process data․ In manual control, human operators interpret sensor data to adjust actuators, ensuring desired outcomes․ Feedback loops are crucial for accuracy, while stability and precision are maintained through continuous monitoring․ These components work together to regulate processes effectively, whether in manual or automated setups․
2․2 Feedback Theory and Linear System Analysis
Feedback theory is central to control systems, enabling stability and accuracy by comparing output to desired input․ In manual control, operators use feedback to adjust system behavior․ Linear system analysis simplifies complex dynamics, allowing predictable responses to inputs․ This analysis is vital for designing stable systems, ensuring precision, and maintaining performance․ Together, feedback and linear analysis form the foundation for understanding and optimizing manual control systems, enhancing reliability and responsiveness in various engineering applications․
2․3 Differences Between Manual and Automatic Control
Manual control relies on human intervention for decision-making and system adjustments, offering flexibility in dynamic situations․ In contrast, automatic control uses predefined algorithms and feedback loops to operate without human input, ensuring consistency and speed․ While manual systems depend on operator expertise and adaptability, automatic systems minimize human error and optimize performance․ Each approach has unique advantages, making them suitable for different applications based on complexity, precision, and operational requirements․
Applications of Manual Control
Manual control is applied in industrial automation, process industries, robotics, aerospace, and telemetric systems, ensuring precise human oversight and adaptability in dynamic operational environments․
3․1 Industrial Automation and Manual Control
Manual control enhances industrial automation by allowing human intervention for precise adjustments and real-time decision-making․ It complements automated systems, ensuring adaptability and reliability in dynamic environments․ Companies like INFOCOM Ltd specialize in integrating manual and automated controls, optimizing industrial processes․ Manual control is crucial in sectors requiring flexibility, such as aerospace and process industries, where human expertise ensures accurate operations and safety․ This blend of technology and human oversight maximizes efficiency and productivity in complex industrial systems․
3․2 Manual Control in Process Industries
Manual control remains integral in process industries, where precise adjustments and real-time oversight are critical․ In chemical plants and manufacturing, human operators ensure process stability and safety, complementing automated systems․ This approach allows quick responses to unexpected variations, enhancing operational reliability․ Industries benefit from the flexibility of manual control, particularly during start-ups or when fine-tuning processes․ It ensures that complex systems operate within desired parameters, maintaining efficiency and product quality․ Manual control’s role is vital, even as automation advances, ensuring seamless process management and adaptability․
3․3 Role of Manual Control in Robotics and Mechatronics
Manual control plays a crucial role in robotics and mechatronics, particularly during system development and operation․ It enables precise adjustments and real-time interventions, ensuring safety and adaptability․ In robotic systems, manual control is used for initial setup, calibration, and troubleshooting․ Operators can override automated functions to address unexpected scenarios, enhancing reliability․ This human-machine collaboration is vital in complex environments, allowing for dynamic decision-making and error correction․ Manual control ensures seamless integration of robotic systems in industries like manufacturing and healthcare, where flexibility and accuracy are paramount․ Its role remains essential despite advancements in automation․
3․4 Aerospace Engineering Applications
Manual control is integral to aerospace engineering, particularly in satellite tracking, antenna alignment, and servo system operations․ Operators use manual adjustments to fine-tune systems for precision and reliability․ In spacecraft and aircraft, manual overrides ensure safety during critical maneuvers․ This human oversight is crucial for real-time corrections and system calibration, especially in dynamic environments․ Aerospace applications rely on manual control for mission-critical tasks, blending human expertise with automated systems to achieve optimal performance and accuracy in high-stakes operations․
Principles of Manual Control Design
4․1 Proportional-Integral (PI) Controllers
PI controllers optimize system performance by adjusting outputs based on proportional and integral terms, minimizing error over time․ Widely used in process industries, they ensure precise control and stability․
Proportional-Integral (PI) controllers are widely used in manual control systems to optimize performance․ They combine proportional and integral terms to adjust outputs, minimizing error over time․ The proportional term reduces steady-state error, while the integral term eliminates offset․ PI controllers are simple, effective, and commonly applied in process industries for temperature, pressure, and flow control․ They offer a balance between responsiveness and stability, making them a preferred choice for engineers․ Regular tuning is essential to ensure optimal performance in dynamic systems․
4․2 Modeling and Simulation of Manual Control Systems
Modeling and simulation are essential tools for analyzing and designing manual control systems; These techniques allow engineers to predict system behavior, test scenarios, and optimize performance without physical implementation․ Simulation software, such as MATLAB and Simulink, enables detailed visualization of dynamic responses․ By creating mathematical models of control systems, engineers can identify potential issues and refine designs․ This approach ensures safety, efficiency, and reliability before real-world application․ Simulation also aids in training operators and validating system modifications, making it a critical step in manual control system development and operation․
4․3 Human-Machine Interface (HMI) Design
Human-Machine Interface (HMI) design is crucial for effective manual control, enabling intuitive interaction between operators and systems․ HMI involves creating user-friendly displays, controls, and feedback mechanisms to enhance operator performance․ Clear visualizations, accessible controls, and real-time data presentation are key design principles․ Effective HMI design reduces errors, improves response times, and enhances overall system reliability․ It also ensures operator safety by providing critical information and alerts․ Advanced HMI solutions integrate touchscreens, alarms, and customizable dashboards to meet specific application needs, making manual control systems more efficient and user-centric․
Case Studies and Real-World Examples
Manual control applications include industrial mixers, telemetric systems, and servo mechanisms․ Real-world examples demonstrate operator involvement in precise, dynamic environments like aerospace and process industries․
5․1 Manual Mixer Operations in Industrial Settings
In industrial settings, manual mixers are operated by skilled personnel to ensure precise blending of materials․ These systems rely on human expertise to adjust parameters like speed and timing, enabling flexibility in production processes․ Operators monitor consistency and quality, making real-time adjustments to achieve desired outcomes․ Manual control in mixers is crucial for custom batches and scenarios where automation may lack adaptability․ This approach balances efficiency with the need for tailored solutions in diverse manufacturing environments․
5․2 Telemetric Control Systems and Their Applications
Telemetric control systems enable remote monitoring and operation of devices through data transmission, blending manual oversight with automated functions․ Widely used in aerospace and industrial automation, these systems allow operators to adjust parameters and respond to real-time feedback․ Applications include satellite tracking, process industries, and robotics, where precise control is essential․ By integrating manual input with telemetry, systems achieve high accuracy and adaptability, ensuring efficient performance across diverse engineering scenarios while maintaining human oversight for critical decisions․
5․3 Servo Systems in Engineering
Servo systems are precise control mechanisms used in engineering to regulate position, velocity, and acceleration․ They rely on feedback loops to maintain accuracy, often integrating manual control for fine-tuning․ In robotics and aerospace, servos enable precise movements, while in industrial settings, they optimize automated processes․ Manual control interfaces allow operators to adjust servo parameters, ensuring adaptability and reliability․ This blend of automation and human oversight makes servo systems indispensable in achieving high-performance engineering solutions across various industries, ensuring both efficiency and accuracy․
Advantages and Limitations of Manual Control
Manual control offers flexibility and adaptability but relies heavily on human expertise, posing risks of error and inconsistency in complex systems․
6․1 Flexibility and Adaptability in Manual Systems
Manual control systems excel in flexibility and adaptability, allowing human operators to adjust processes dynamically in response to changing conditions․ This makes them ideal for scenarios requiring real-time decision-making and customization․ Unlike automatic systems, manual control enables operators to improvise and handle unexpected issues without extensive reprogramming․ Industries like industrial automation and process control benefit from this adaptability, as humans can fine-tune operations to meet specific demands․ However, this reliance on human expertise also introduces variability, as performance depends on the operator’s skill and experience․ Despite this, manual systems remain cost-effective for smaller-scale or variable applications․
6․2 Limitations of Human Intervention in Control Systems
Human intervention in manual control systems introduces limitations such as potential errors, fatigue, and slower response times compared to automated solutions․ Operators’ performance can vary due to stress, training, or workload, impacting system reliability․ Additionally, manual systems often lack scalability, making them impractical for complex or large-scale operations․ Despite these challenges, manual control remains essential for tasks requiring nuanced decision-making, highlighting the need for balanced integration with automated systems to optimize performance and reduce risks․ This duality underscores the ongoing role of human expertise in modern engineering․
6․3 Cost-Benefit Analysis of Manual vs․ Automatic Control
Manual control systems often require lower initial investment but incur higher operational costs due to human labor and potential errors․ Automatic systems, while expensive to install, offer long-term savings through reduced personnel needs and enhanced efficiency․ Scalability and reliability also favor automatic systems, though manual control provides flexibility in unique or unpredictable scenarios․ The choice depends on system complexity, operational demands, and budget constraints, balancing upfront costs with long-term benefits and maintenance requirements․
Tools and Technologies in Manual Control
Manual control systems utilize tools like SCADA systems, programmable logic controllers, and HMI interfaces, enabling real-time monitoring and precise adjustments in industrial and mechanical processes efficiently․
7․1 Software Solutions for Control System Design
Software tools like MATLAB, Simulink, and LabVIEW are essential for designing and analyzing manual control systems․ These platforms offer simulation environments, enabling engineers to model and test system dynamics․ They provide advanced algorithms for tuning controllers, such as PI and PID, ensuring optimal performance․ Additionally, SCADA systems and HMI interfaces are integrated into these software solutions, allowing real-time monitoring and control․ These tools enhance precision, reduce errors, and streamline the development process in industrial automation and mechanical engineering applications․
7․2 Hardware Components in Manual Control Systems
Manual control systems rely on physical hardware components such as sensors, actuators, and control panels․ Sensors detect system parameters, while actuators execute commands․ Interfaces like buttons, joysticks, and switches enable operator input; Programmable logic controllers (PLC) and human-machine interfaces (HMIs) are integral, providing real-time monitoring and adjustments․ These components ensure precise control, enabling operators to respond dynamically to system changes․ Hardware redundancy and fail-safe mechanisms are often implemented to enhance reliability and safety in industrial and mechanical systems․
7․3 Emerging Technologies in Manual Control
Emerging technologies are transforming manual control systems, enhancing efficiency and precision․ IoT integration enables real-time data exchange and remote monitoring, while AI and machine learning optimize decision-making processes․ Advanced HMI designs improve user experience, and wearable technologies provide hands-free control․ Robotics and mechatronics are increasingly incorporated, offering improved accuracy․ These innovations ensure manual control remains relevant and adaptive in modern engineering, bridging the gap between human expertise and automated systems for superior performance and reliability across industries․
Safety and Reliability in Manual Control
Safety and reliability in manual control are ensured through fail-safe mechanisms, redundancy, and human factors analysis, minimizing risks and ensuring system integrity and dependability․
8․1 Risk Assessment in Manual Control Systems
Risk assessment in manual control systems involves identifying potential hazards and evaluating their impact․ This process ensures the implementation of safety measures and reduces operational risks․ Engineers analyze human error probabilities, equipment reliability, and environmental factors to predict failure points․ By prioritizing critical risks, they design fail-safe mechanisms and training programs to enhance system reliability and operator performance, ensuring safe and efficient manual control operations across various industries․
8․2 Fail-Safe Mechanisms and Redundancy
Fail-safe mechanisms ensure systems revert to a safe state during failures, minimizing risks․ Redundancy involves duplicating critical components to maintain functionality if primary systems fail․ These strategies are crucial in manual control systems, where human intervention is frequent․ Fail-safe designs include emergency shutdowns and backup power supplies, while redundancy ensures continuous operation․ Together, they enhance reliability and safety, addressing potential errors in manual oversight and equipment malfunctions․ These measures are vital for maintaining operational integrity in industries reliant on manual control systems․
8․3 Human Factors in System Reliability
Human factors significantly influence system reliability in manual control․ Operator training, workload, and situational awareness are critical․ Fatigue, stress, and cognitive biases can impair decision-making, leading to errors․ Effective Human-Machine Interfaces (HMIs) reduce complexity, while clear procedures and alarms enhance response accuracy․ Regular training and ergonomic design minimize human error, ensuring reliable system performance․ Addressing these factors is essential for optimizing manual control systems’ safety and efficiency, as human reliability directly impacts overall system dependability and operational success․
Integration with Automatic Control Systems
Manual control seamlessly integrates with automatic systems, combining human expertise with automation for enhanced efficiency․ This hybrid approach ensures adaptability and precision, optimizing complex operations effectively․
9․1 Hybrid Control Systems: Combining Manual and Automatic
Hybrid control systems merge manual and automatic operations, offering flexibility and precision․ These systems enable operators to intervene when necessary, while automation handles routine tasks․ This integration enhances adaptability, ensuring efficient performance across various engineering applications․ By combining human expertise with automated processes, hybrid systems optimize productivity and reliability, making them ideal for complex environments where both precision and adaptability are crucial․
9․2 Transitioning from Manual to Automatic Control
Transitioning from manual to automatic control enhances efficiency and consistency, reducing human error․ This shift involves implementing advanced technologies and training personnel to manage automated systems․ While initial costs and system integration pose challenges, the long-term benefits of increased productivity and reliability often justify the investment․ Hybrid systems, combining manual and automatic elements, serve as a bridge during this transition․ Industries like manufacturing and aerospace leverage this approach to maintain operational flexibility while embracing modern advancements, ensuring safety and adaptability in evolving engineering environments․
9․3 Supervisory Control and Data Acquisition (SCADA)
SCADA systems integrate manual and automatic control, enabling real-time monitoring and remote management of processes․ They collect data from sensors, analyze it, and execute commands to maintain optimal operation․ SCADA is widely used in industries like energy and water management, offering centralized control and redundancy․ Operators can manually override automated functions during critical situations, ensuring adaptability and safety․ SCADA enhances reliability by providing fail-safe mechanisms and historical data analysis, making it a crucial tool for modern engineering and industrial automation applications․
Education and Training in Manual Control
Academic programs, certifications, and workshops provide foundational knowledge and practical skills in manual control, preparing engineers to design and manage systems effectively in real-world applications․
10․1 Academic Programs in Control Systems Engineering
Academic programs in control systems engineering offer comprehensive studies in manual control principles, feedback theory, and system design․ These programs, available at both undergraduate and graduate levels, integrate theoretical knowledge with practical applications, equipping students with skills to analyze and optimize control systems․ Many universities incorporate lab experiments and simulations, such as those using proportional-integral (PI) controllers, to provide hands-on experience․ Courses often emphasize interdisciplinary approaches, combining mechanical, electrical, and aerospace engineering concepts to prepare students for real-world challenges in manual control environments․
10․2 Professional Certifications and Licensing
Professional certifications and licensing are crucial for engineers specializing in manual control systems․ Certifications like the Professional Engineer (PE) license, offered by the National Council of Examiners for Engineering and Surveying (NCEES), validate expertise in control systems engineering․ Additionally, certifications from organizations like the International Society of Automation (ISA) provide specialized knowledge in areas such as automation and control․ These credentials ensure professionals meet industry standards and are equipped to handle complex manual control applications across industries like aerospace, industrial automation, and robotics․
10․3 Practical Training and Workshops
Practical training and workshops are essential for mastering manual control systems, offering hands-on experience with real-world applications․ These sessions often include simulations, lab experiments, and case studies, allowing participants to troubleshoot and optimize systems․ Workshops frequently involve collaboration with industry experts, providing insights into best practices and emerging technologies․ Such training enhances problem-solving skills, ensuring engineers can effectively manage manual control systems in diverse engineering fields, from industrial automation to aerospace․ These interactive learning environments are critical for developing proficiency in manual control operations․
Future Trends in Manual Control
Future trends include integrating AI, machine learning, and IoT for enhanced precision and efficiency in manual control systems, ensuring adaptability to modern engineering challenges and sustainability goals․
11․1 The Role of AI and Machine Learning
AI and machine learning are transforming manual control by enabling predictive analytics and adaptive systems․ These technologies optimize human-machine interactions, enhancing decision-making accuracy and operational efficiency․ AI-driven algorithms can analyze vast data sets, identify patterns, and recommend optimal control strategies․ Machine learning enables systems to learn from operator inputs, improving performance over time․ Integration of AI in manual control systems allows for real-time adjustments, reducing errors and increasing reliability․ This synergy between human expertise and AI capabilities paves the way for smarter, more responsive control solutions in various engineering domains․
11․2 Internet of Things (IoT) and Manual Control
The Internet of Things (IoT) enhances manual control by enabling real-time data exchange and connectivity across devices․ IoT integrates sensors, actuators, and control systems, allowing operators to monitor and adjust processes remotely․ This connectivity improves decision-making and reduces response times․ IoT also facilitates predictive maintenance and resource optimization, making manual control more efficient․ In industries like manufacturing and aerospace, IoT-enabled manual systems ensure precise operations and scalability․ By bridging physical and digital worlds, IoT transforms manual control into a more agile and responsive solution for modern engineering challenges․
11․3 Sustainability and Green Engineering
Manual control plays a pivotal role in advancing sustainability and green engineering․ By allowing precise adjustments, manual systems optimize resource usage, reducing energy consumption and waste․ Operators can implement eco-friendly strategies, such as minimizing material inputs and lowering emissions․ Green engineering integrates manual control with sustainable practices, promoting environmentally responsible solutions․ This approach supports long-term ecological balance while maintaining operational efficiency․ Manual control’s adaptability ensures compatibility with emerging green technologies, fostering innovation in sustainable design and process management across various industries․
Professional Resources and References
Key resources include textbooks like Dorf’s Modern Control Systems and Franklin’s Feedback Control․ Industry standards from IEEE and IEC provide essential guidelines․ Professional certifications, such as the PE license and ISA/CSIA certifications, are crucial for engineers․ Academic journals like IEEE Transactions on Automatic Control and Control Engineering Practice offer cutting-edge research․ Online forums and communities, like LinkedIn groups, facilitate knowledge sharing․ Manufacturer resources, such as Siemens and Rockwell Automation manuals, offer practical insights․ Workshops and webinars by industry leaders complement theoretical learning, ensuring comprehensive understanding and application of manual control principles․
12․1 Control Systems Engineering Exam Reference Manual
The Control Systems Engineering Exam Reference Manual by Bryon Lewis is a comprehensive guide for engineers preparing for the PE exam․ It covers fundamental concepts, practical applications, and industry standards, with a focus on manual control systems․ The manual includes detailed explanations of control theory, system design, and real-world case studies․ It emphasizes the importance of understanding feedback mechanisms, PID controllers, and system stability․ This resource is invaluable for professionals seeking to master manual control principles and apply them effectively in engineering practice․
12․2 Industry Standards and Regulations
Industry standards and regulations play a critical role in ensuring the safety, reliability, and efficiency of manual control systems․ Organizations like ISA and IEEE establish guidelines for system design, operation, and maintenance․ These standards address safety protocols, documentation requirements, and compliance with legal frameworks․ Adhering to these regulations minimizes risks and ensures uniformity in system performance across industries․ Professionals must stay updated on evolving standards to maintain operational excellence and legal compliance in manual control applications․
12․3 Key Textbooks and Online Resources
Essential textbooks like “Control Systems Engineering” by Norman S․ Nise and “Modern Control Systems” by Dorf provide foundational knowledge․ Online platforms such as Access Engineering offer interactive learning tools and updated resources․ The ISA Exam Reference Manual is crucial for professionals preparing for certifications; These resources cater to both academic and practical needs, ensuring comprehensive understanding and application of manual control principles in various engineering disciplines․
Leave a Reply
You must be logged in to post a comment.